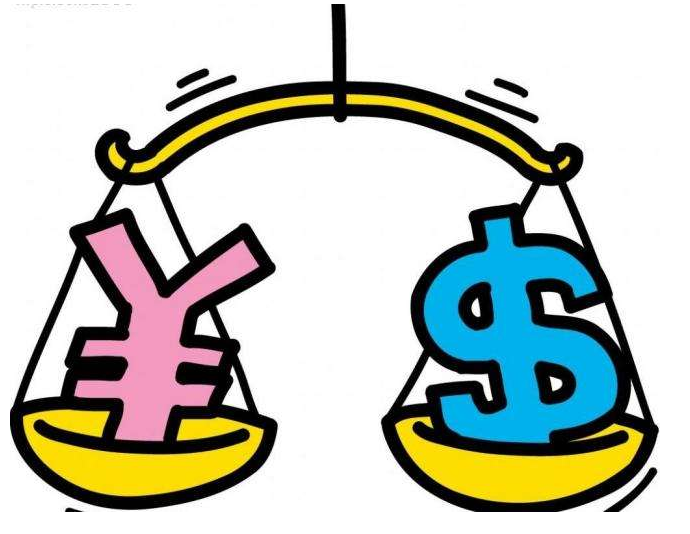
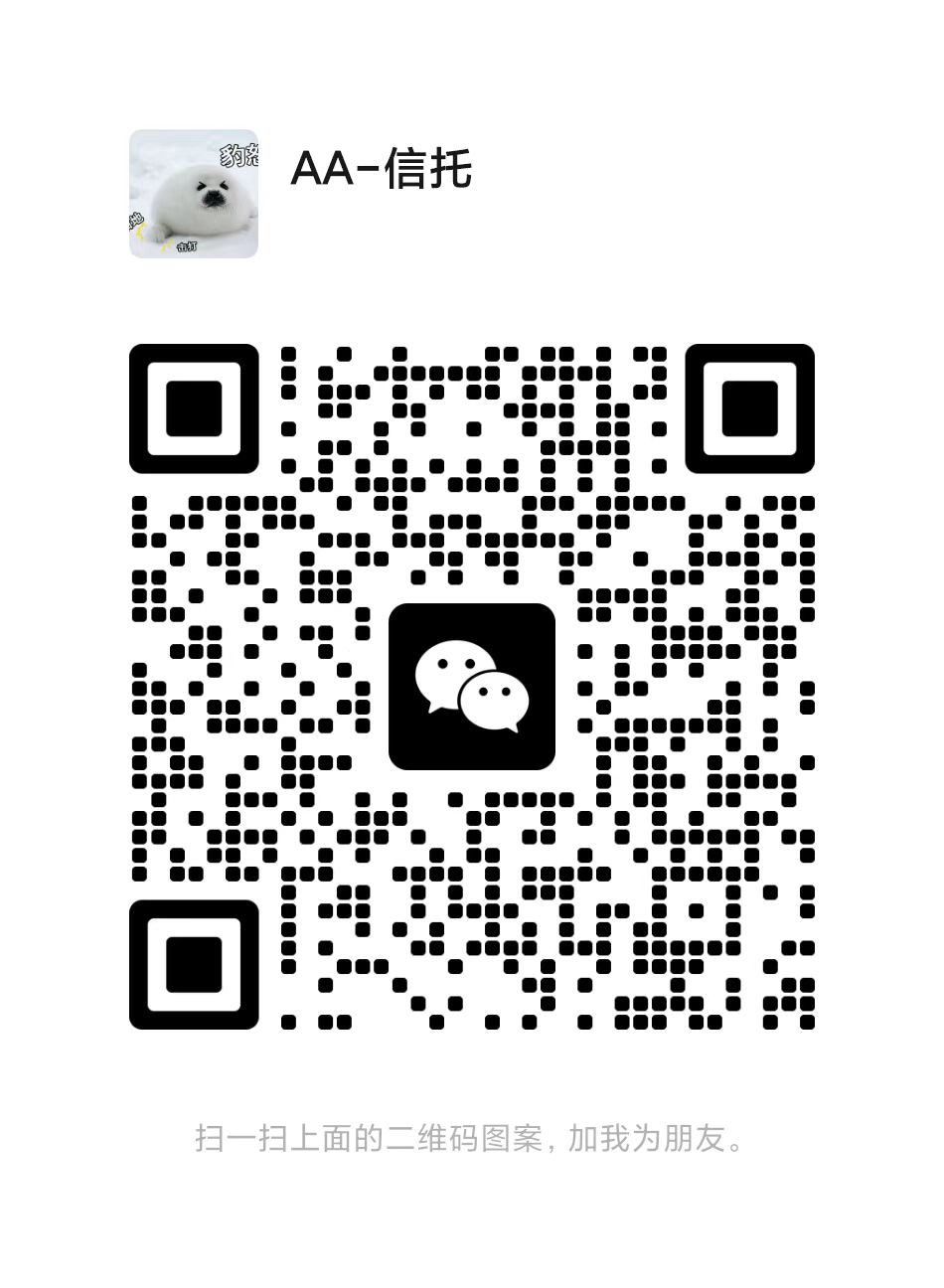
添加微信好友, 获取更多信息
复制微信号
河南林州LZ
稳健区域政信,HQQ精神、扁担精神的发祥地!!AA发债主体融资+AA发债主体担保!!2022年全市GDP 657.44亿元,同比增长4.80%,一般公共预算收入43.54亿元,负债率仅12.46%,经济基本面良好!!
【2023年林州城投债权转让计划】
拍卖总规模:2亿(分期发行)
存续期:
一期、二期(12个月)30-50-100-300 9.0%-9.3%-9.5%-9.8%
付息方式:每日成立,季度付息(每年的3、6、9、12月的20日付息)
认购金额:30万起投(每个自然日成立起息),10万元的整数倍递增
用途:用于补充流动资金。
【融资方】林州市城市投资集团有限公司,成立于2011年,注册资本8.75亿元,实控人是林州市财政局,主体评级AA、债券评级AAA(存续债券2只”20林城01,21林城01“,存量规模6亿)公司是林州市重要基础设施建设主体,业务持续性仍较好,外部支持力度大,2021年林州市财政局向公司注入货币资金2.00亿元。至2021年底,公司总资产178.14亿,同比增长18.6%;总营收45.18亿,增长138%,(主要是销售业务、2个PPP项目的完工所致)净利润1.18亿。
2023年林州城投债权转让计划
新闻资讯:
遵守养护施工的规章制度和技术规范2、负责所辖段桥梁、路基、路面、交通安全设施、绿化等日常养护管理工作
3、负责所辖段养护专项工程、大中修工程的监督管理工作
4、参与养护工程的交、竣工验收工作,负责所辖段养护专项工程的计量核定上报工作
5、负责所辖段路面、桥涵及附属设施的调查、检测,逐步建立养护管理技术档案数据库系统
6、负责养护设备的建档、使用和管理工作
7、负责所辖段路面除雪、水毁修复等应急处理工作
8、完成上级领导交办的其它工作
本文以曲阜轨道板场CRTSⅡ型无砟轨道板制造为例,介绍CRTSⅡ型无砟轨道板场规划布置和预制、打磨生产
【关键词】 CRTSⅡ型,轨道板场规划,预制,打磨 1 前言 伴随着中国高速铁路跨越式发展,无砟轨道技术得到了不断完善和飞速发展
与有砟轨道板相比,其具有轨道稳定性高、平顺性好、结构耐久性强、维修工作量显著减少、列车安全性和舒适性显著提高等优点;其具有结构稳定,利于工厂化生产,利于提高施工效率等特点
2 工程概况 曲阜轨道板场共计生产CRTSⅡ型无砟轨道标准板23878块
标准板长6.45m,宽2.55m,厚0.2m(详见图1 CRTSⅡ型轨道板结构图),为横向先张预应力混凝土结构
纵向设置10对承轨道台,承轨台间设置横向预裂缝;横向每个承轨台配有6根Φ10 mm预应力筋,纵向配有6根20mm精轧螺纹钢筋,板与板之间通过张拉锁和精轧螺纹钢筋连成整体
3 曲阜轨道板场规划 轨道板在厂房内集中预制,实行工厂化施工管理
毛坯板采用先张法长线台座法生产,设两条生产线,每条生产线作业周期为24小时(其中作业时间8h,养护时间约16h),生产能力41块;采用两班作业制,每天生产毛坯板82块;成品板生产线以数控磨床为中心,采用三班作业制,每班打磨27-36块,每天打磨81-108块;设置4个月成品板储存区,1个月毛坯板储存区,最大存板能力约12000块
4 施工工艺 4.1 施工工艺流程 CRTSⅡ型无砟轨道板施工工艺流程详见图2
4.2钢筋网片制作 在轨道板内依次布置有Ф5mm预应力筋、下层钢筋网片、Ф10mm预应力筋及上层钢筋网片
Ф5mm和Ф10mm预应力筋在场内采用定长切割机进行下料
上、下钢筋网片在定型胎具上绑扎,通过横移小车运送至制板车间进行安装
轨道板内预应筋及上下层钢筋网片各层的交点均通过环氧涂层、绝缘热缩套管、绝缘垫片进行了绝缘处理
4.2.1钢筋加工 钢筋网片主要包括Φ8mm结构钢筋、Φ8mm环氧涂层钢筋、Φ16mm接地钢筋、Φ20mm精扎螺文钢筋
除Φ8mm结构钢筋进场为盘圆外,其余均为定尺寸加工
绝缘热缩管安装在专用胎架上进行,比照标准件将绝缘热缩管穿入φ20精轧螺纹钢和φ16接地钢筋上,精确定位后进行加热
加热时,喷火与绝缘热缩管保持10~15cm的距离,移动速度控制在1m/s,直至热缩管处钢筋螺纹痕迹露出1~2mm,热缩管颜色不发黄为止
接地端子及接地扁钢焊接在下层钢筋绑扎胎具上进行
接地端子采用单面焊焊缝长度不小于100mm,接地扁钢与φ16接地钢筋采用双面满焊
4.2.2上、下层钢筋网片绑扎 上、下层钢筋网片在专用胎具上进行绑扎,将结构钢筋放置在绑扎胎具纵向定位凹槽中,再将环氧树脂涂层钢筋放入横向定位凹槽中,纵、横向钢筋通过绝缘垫片、绝缘热缩管进行绝缘,采用绝缘绑扎丝进行绑扎
4.2.3钢筋网片绝缘检测 钢筋网片绑扎完成后采用500V兆欧表对网片进行绝缘检测,检测前对电阻仪进行调零处理,然后检测每根横向钢筋与相连的纵向钢筋间电阻值
若电阻值大于2MΩ,则绝缘电阻检测合格,否则,需查明原因并进行处理
4.3模具检测与清理 4.3.1模具检测 ⑴模具安装完成经检验合格后方可投入使用,在使用中对模具进行检查,并记录检查结果
①日常检查:每次脱模后进行日常检查
日常检查包括模具的外观、平整度
②定期检查:在每个月对所有模具进行一次检查,检查采用全站仪、电子水准仪、游标卡尺、球形棱镜、钢板尺等仪器工装,主要检查:长度、宽度、厚度、承轨槽细部尺寸、平整度及模具间高度偏差等
⑵模具尺寸对轨道板形状、尺寸及预埋件位置有很大影响,其尺寸允许误差如表1所示
表1 模具尺寸允许误差 4.3.3模板清理 脱模后采用刮刀、工业吸尘器将模具上的杂物清理干净,然后均匀喷涂脱模剂
注意检查承轨槽、橡胶端模安装处、橡胶端模、预裂缝等表面脱模剂是否喷涂均匀
4.4 钢筋网片安装 4.4.1 预应力筋制作 轨道板内布置有6根Ф5mm定位预应力筋和60根Ф10mm预应力筋,预应力钢筋采用钢筋定长切断机切断
制作好的预应力筋长度误差控制在±10mm内
4.4.2预应力筋及钢筋网片安装 将6根φ5mm预应力筋安放在V型槽中,采用专用工具锚固定在横梁上,外露长度控制在10~20mm
采用桁车将下层钢筋网片依次安放在定位筋上方的相应位置,接地端子位置和定位销位置相对应
下层钢筋安装完成后,人工按每3根一批将φ10mm预应力筋放入模具内
先将预应力筋一端采用锚具固定在横梁上,使其外露长度控制在10~20mm,梳理拉紧后固定另一端至相对横梁上,其外露长度不小于10mm
预应力筋张拉分两个阶段,先初张拉至20%,安装分丝隔板后终张拉至100%
20%初张拉采用伸长量控制,张拉力校核
终张拉以张拉力控制,伸长值做校核
实际张拉力及伸长值与设计值偏差不得超过5%
张拉过程中,始终保持同端千斤顶活塞伸长值间偏差不大于2mm,异端千斤顶活塞伸长值间偏差不大于4mm
预应力筋终张拉完成后,人工配合桁车将检测合格的上层钢筋网片吊入模具中
钢筋安装完成后,对钢筋的保护层厚度、安装位置偏差、绝缘电阻等进行检查
4.5 混凝土作业 1)混凝土采用全自动拌和机生产,电瓶车装载料斗运输
2)混凝土布料机从生产线的一端到另一端,依次、连续、均匀地将混凝土浇筑入模,混凝土浇筑方向垂直于布料机的行驶方向,同时以每块模板为独立单元启动振动装置,将混凝土密实成型
3)混凝土分三次布料,第一次注入到分丝横隔板处;第二次注入板高的80%;第三次注入剩余混凝土
4)在第一层混凝土布料完成后,开始振捣,直至第三层布料结束后停止,振捣至混凝土表面泛浆后,气泡不持续涌出为准
5)刮平:放下整平板,布料机向前运行,将混凝土表面刮平,并将多余混凝土刮到相邻模具内
6)刷毛:在混凝土初凝前,移动刷毛机到模具纵向挡板上,控制毛刷与轨道板接触深度在1mm~2mm,依次对轨道板进行刷毛作业
7)调高装置安装:刷毛完毕后,按设计要求在轨道板的相应位置安装调高预埋板
8)拆除分丝横隔板:在每块轨道板混凝土浇筑完成2~3小时后,人工配合桁车拆除分丝横隔板
9)覆盖养护:在混凝土刷毛完毕后覆盖塑料养护膜,分丝横隔板拆除后,再覆盖专用养护膜
4.6毛坯板脱模及存放 4.6.1 预应力筋放张与切割 当同步养生试件抗压强度达到48MPa,且轨道板表面温度与周围环境温度不大于20℃时,进行预应力筋放张和切割作业
放张作业完成后,开始切割预应力筋
预应力筋切割采用切割小车进行,先切断在张拉台座1/2处模板间的预应力筋,再切断在张拉台座1/4和3/4处模板间的预应力筋,最后切断其余模板间的预应力筋
4.6.2 轨道板脱模 脱模采用桁车配真空吊具进行
将真空吊具移到要脱模的轨道板上方,调整桁车位置,降低吊具高度使吸盘落到轨道板混凝土表面固定区域,启动真空泵,使吸盘紧紧吸附于混凝土表面上,直到达到预先设定好的吸附力
在真空吊具调平之后,开启压缩空气系统,通过模具底部的6个入风口吹入压缩空气
将轨道板平稳地从模具中吊出
4.6.3轨道板存放 人工将4块垫木按设计位置摆放在存板台上
采用龙门吊运送毛坯板至存放位置,对准4个存放支点后,将毛坯板放置在垫木上
在存板期间,每周对毛坯板存放台座进行一次检查,内容包括:垫木的支承情况、存板台地基沉降情况、板垛垂直状态等
4.7轨道板打磨、安装扣件 4.7.1毛坯板翻转 毛坯板翻转由特制的翻转机完成,其作业程序如下: 1)启动翻转机,将翻转装置下降到极限位置,并打开锁紧装置
2)用龙门桥式起重机将毛坯板放到翻转框架上
3)启动翻转机液压装置,将毛坯板夹紧
4)将翻转装置上升到极限位置,并翻转180°
5)将翻转装置下降到极限位置后,解开翻转机锁紧装置
6)用滚轮运输线将毛坯板运送到打磨工位
4.7.2轨道板预应力筋余头切割 运进打磨工位前,对毛坯板两侧预应力筋余头进行切割
4.7.3轨道板打磨 轨道板打磨由数控磨床完成
1)数据输入:将设计单位提交的线路设计资料输入计算机控制系统
2)固定轨道板:托架线将轨道板运送到打磨工位,通过4个油缸将轨道板顶起并进行找平调整,最后用6个油缸从侧面将轨道板卡紧
即可开始磨削加工
3)生成子程序:通过系统测量传感器测量轨道板的各个关键点,计算出板平面相对于加工面的位置,然后将加工面转换到轨道板上,并借助路线控制数据(每个承轨台的Y、Z坐标和倾斜角)自动生成加工该块轨道板的数控子程序
4)打磨:根据给定值,对轨道板进行多个粗磨行程和一个精磨行程,直至符合质量标准
5)清洗出板:用固定在机床架梁冲洗装置冲洗轨道板
4.7.4安装扣件 打磨后,由托架线运输到扣件安装工位
在此,要对轨道板进行套管销孔干燥、注射油脂、安装扣件等作业
4.7.5成品板绝缘检测 成品板绝缘检测使用ZL5-LCR智能测量仪
将轨道板运至测量架正下方,由电动平车将轨道板顶起使轨垫与检测钢轨底面紧贴,最后进行绝缘检测
4.7.6产品标识 每块轨道板相对应于线路上一个固定位置,经质量检验合格后,系统将自动在轨道板上铣出识别号码
4.8成品板存放 采用运输车将轨轨道板运至成品板存放区进行存放
存放垫块顶面高差不大于2mm,且每垛成品板不超过9层,每层上下对齐
5 主要机械设备配置 CRTSⅡ型轨道板生产主要设备参见表2
6 结束语 在国内,CRTSⅡ型无砟轨道板应用时间较短,生产技术和生产功效还存在一定不足,还需通过不断技术研究,使CRTSⅡ型无砟轨道板生产技术更加成熟,生产功效不断提高,为中国铁路无砟轨道系统进一步发展做出贡献